|
|
Job Location: Waco, TX
|
|
ABOUT THE ORGANIZATION: The Envases Group is a worldwide supplier of quality packaging solutions. The Envases Group is divided into three packaging divisions - PET Packaging, Aluminum Beverage Packaging and Food & Industrial Packaging - each with special competences within their field to serve customers the best way possible. Our core value is to supply high quality packaging solutions, always striving for growing our business in order to be the market leader in the markets we operate in. Envases Group is expanding global presence by the plan to open its first aluminum beverage can production and distribution center in Waco, Texas. The Waco operation will focus on aluminum beverage containers commonly used for soft drinks, beers, energy drinks, teas and non-carbonated beverages. Thank you for having interest in our employment opportunities.
REQ NUMBER: MAN-21-00031
CATEGORY: Manufacturing
EXEMPT/NON-EXEMPT: Exempt
FULL-TIME/PART-TIME: Full-Time
NUMBER OF OPENINGS: 2
SHIFT: Days
POSITION: Production Supervisor
Description
POSITION SUMMARY: The Front End/Back End Supervisor is responsible for the unit operating performance to include production, raw material usage, energy usage, quality, daily performance tracking, troubleshooting, and basic unit optimization. The Front End/Back End Supervisor adds direct value to the business by driving real-time unit performance in these areas. Responsible for first-line direction of non-exempt employees involved in production, treating, printing, finishing, and other line operations. Reviews production schedules, material and manpower resources. The Front End/Back End Supervisor provides direction to team members (technicians and operators) to ensure the operations are conducted safely, timely and efficiently. The position will ensure operations are maximized to deliver all production objectives, sustain quality and attain output requirements. The position will assist in establishing and modifying the operational methods and processes by recommending changes or maintenance. The position will assist with maintaining a variety of reports and records, production documentation, information related to operation scheduling and performance.
ESSENTIAL JOB FUNCTIONS: - Hands on supervisory position in which an individual is expected to provide assistance to the Production Manager as well as acting as a technical subject matter expert for the line operations; direct job assignments and provide technical hands on leadership to the production staff
- Demonstrates leadership in driving corporate zero-incident safety culture through safe work practices and operator engagement
- Develop excellent, collaborative working relationships with Operations, Manufacturing, Production & Process Engineering, Reliability, Quality Assurance, Production Planning, & other support groups
- Develops a team to solve day-to-day operational issues and reach short- and long-term performance goals
- Tracks key performance indicators/costs, anticipating and correcting trends that would compromise the achievement of financial targets
- Directly operate or supervise the operation of the whole production line, lead all staff in the shift, including contract workers
- Monitor and maintain proper safety requirements in the shift to ensure the safety of the staff
- Monitor and maintain the quality to ensure the products meet the required standards
- Provide training to the staff on relevant environmental health and safety requirements to ensure that all staff are trained in accordance with regulations
- Achieve operating performance targets and improvements including cost reductions, reduced cycle times and reduced lead times.
- Accountable for providing accurate shipment forecasts and achieving forecast.
- Oversees and ensures facility equipment reliability to minimize downtime
- Coaches operators through the problem solving process to identify problem areas and solve them, including manufacturing processes, reducing set up time, equipment problems and reducing scrap
- Regularly monitors order volume and performs capacity analysis and workforce adjustments to maximize labor utilization
- Monitoring manufacturing of customer orders for timely shipment and workforce capacity analysis
- Continually identifies and implements short and long term cost savings opportunities, in production operations that do not compromise quality
- Convey a professional attitude towards other employees while recognizing the responsibility to meet production schedules
- Assist and train maintenance, production or other technicians as needed with technical or troubleshooting related matters
- Ability to work in a team environment, record data in a computer system, communicate with multiple departments, and complete work orders and preventative maintenance on equipment indoors and outdoors
- Participate in the safety programs and/or committees; follow all site safety policies, company policies and procedures work safely and wear appropriate PPE
- Effectively communicating and engaging with other functional groups at all levels from craft persons and operators to plant leadership
- Provides overall management of the production operations team ensuring overall safe performance of machining and personnel operations while sustaining quality of product and timely distribution
- Responsible for monitoring the daily production of assemblers and machine operators
- Trains operators on procedures, methods, problem solving, prints, programming, quality requirements, team methods and safety
- Educates operators in the safety requirements of their department and plant
- Coaches operators on safety improvements, department inspections, safety surveys and follow up on safety issues
- Works with operators on quality assurance, including quality requirements and procedures for the department and plant, as well as monitoring quality
- Manage and lead the team, ensuring adequate staffing levels, managing holiday allowances, recruitment, training, development, appraisal, attendance, disciplinary issues and daily supervision to maximize efficient productivity
- Motivate and coach the team to operational success
- Assess employee performance; provide positive and constructive feedback; provide conflict resolution; complete annual performance review process; address performance issues with corrective actions in performance improvement plans or through disciplinary actions; monitor the completion of tasks and ensure good performance and record on appropriate systems
- Apply qualitative and quantitative methods to measure team effectiveness and performance
- Consistently promote high standards through personal example and roll out through the team so that each member of the team understands the standards and behaviors expected of them
- Review, implement and update company records e.g. training matrices, performance reviews, risk assessments
- Lead the team in new product and process introduction
- Provide scheduling details, any needed instructional guidance of job assignments, correct procedures and applicable techniques to perform specific skills; ensure accuracy and completion
POSITION REQUIREMENTS: EDUCATION & EXPERIENCE: - Required - Bachelor's Degree in Mechanical Engineering, Industrial Engineering, Chemical Engineering or Mechanical Electrical Engineering or related field
- Minimum 1 year of demonstrated leadership experience required; prior supervisory experience in a manufacturing environment a plus
- Minimum 1 years' experience serving as an engineer in a metalworking industry, industrial maintenance, manufacturing or food industry; prefer 2-3 years' experience in production, industrial or warehouse management
- Strong foundation in statistical process control, engineering change control and process release strategies, required
- Project management experience, preferred
- Demonstrated ability to perform in a 24-hour / 7-day week continuous operation
- Prefer experience in maintenance and repair of machining/manufacturing systems or experience in an industrial continuous process manufacturing environment
GENERAL SKILLS/EXPERIENCE: - Good level of assertiveness to challenge and support the team
- Working knowledge & understanding of statistical process control tools and statistical analysis
- Working knowledge of Quality Management Systems, Lab equipment and Control Plans
- Working knowledge & understanding of engine and equipment technical manuals, as well as, knowledge and understanding of typical engine instrumentation and control systems
- Working knowledge of refractories, including installation and application
- Understanding engineering, scientific and other technical information
- Demonstrated ability of budgeting and cost control
- Work requires the ability to perform complex engineering computations
- Working knowledge of all automation standard practices
- Ability to read and interpret P&ID drawings, pneumatic, hydraulic and electrical schematics for use in system understanding and troubleshooting
- Strong organizational skills and proven ability to maintain accurate, detailed records that will be audited periodically; Ability to work on multiple projects at once with tight deadlines
- Must be able to identify and execute improvement opportunities through both process improvements and system improvements
- Travel required for training and to regularly conduct business with and meet with vendors/suppliers
- Must be a self-starter and have the desire and ability to take ownership and responsibility with little direction
- Ability to be pragmatic in decision making; requires high integrity
- Ability to work with employees from many different cultures and backgrounds
- Preference will be given to qualified local candidates
SOFTWARE/COMPUTER SKILLS & EXPERIENCE: - General knowledge of basic hardware and software and uses of a variety of different computer operating systems such as Microsoft Office Work, Excel, Outlook, Google Workspace, and web-site software
- PLC user or programming experience is a plus
- Knowledge of SolidWorks and AutoCAD preferred
- Knowledge in Data Acquisition concepts, hardware, and interfacing
DISCLAIMER: The above statements are intended to describe the general nature and level of work being performed by people assigned to this job. They are not intended to be an exhaustive list of all responsibilities, duties, and skills required of personnel so classified. Management maintains the right to assign or reassign duties and responsibilities to this job at any time. HOURS / SPECIAL CONDITIONS: 12 hour rotating shifts 4 days on and 4 days off; Rotating shifts requires working night shifts; Present to fulfill job duties & meet operational demands/support; Schedule may vary depending on plant operational needs thus flexibility is required which may include long days, evenings, weekends, holidays and overtime; Regular and predictable attendance is an essential function of this position. PM21
EOE STATEMENT: Envases Commerce LLC. is an equal opportunity employer and prohibits employment discrimination practices. All qualified applicants will receive consideration for employment without regard to race, color, religion, sex, national origin, disability status, protected veteran status or any other characteristic protected by law.
PI143201789
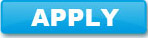
|
|
See all jobs in Waco TX
|